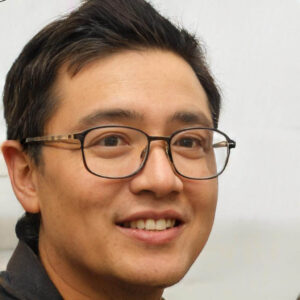
By Michael Zhang || Updated on 26th Feb March 2024
Michael Zhang is a seasoned professional with 15 years of experience in the solar lights industry. Throughout his career, he has been actively involved in product design and developing, gaining valuable expertise and insight into the industry. Known for his dedication and professionalism, Michael has contributed significantly to the growth and success of various solar lights projects. His extensive knowledge and hands-on experience make him a trusted authority in the field, and he continues to innovate and excel in his role.
These solar panels, green new energy, the future energy main force, Do you know how it was formed? Let’s start with these stones. Silica ore is the main raw material for solar panels,It’s like smelting iron ore into steel. The process of making steel should not be unfamiliar to you. Just like iron ore is made into steel. Only the equipment used to make silicon crystals from silicon ore looks a bit more high-tech.
Table of Contents
Step 1: Turning Silicon Ore into Silicon Crystals
After all, silicon is more valuable than iron, The refining technology is more advanced. Silicon ore is put into the special equipment and heated up.
Anyway, through a special and complicated process. To extract the silicon crystals. The final result is this black stuff. Silicon crystals that look like rockets. Then we use special cutting equipment. The black silicon crystals are cut. The cutting equipment is also very high-tech. It can be cut into different shapes according to different needs.This step completes the transformation from silicon ore to monocrystalline silicon to silicon wafers.
The next step is even more critical.
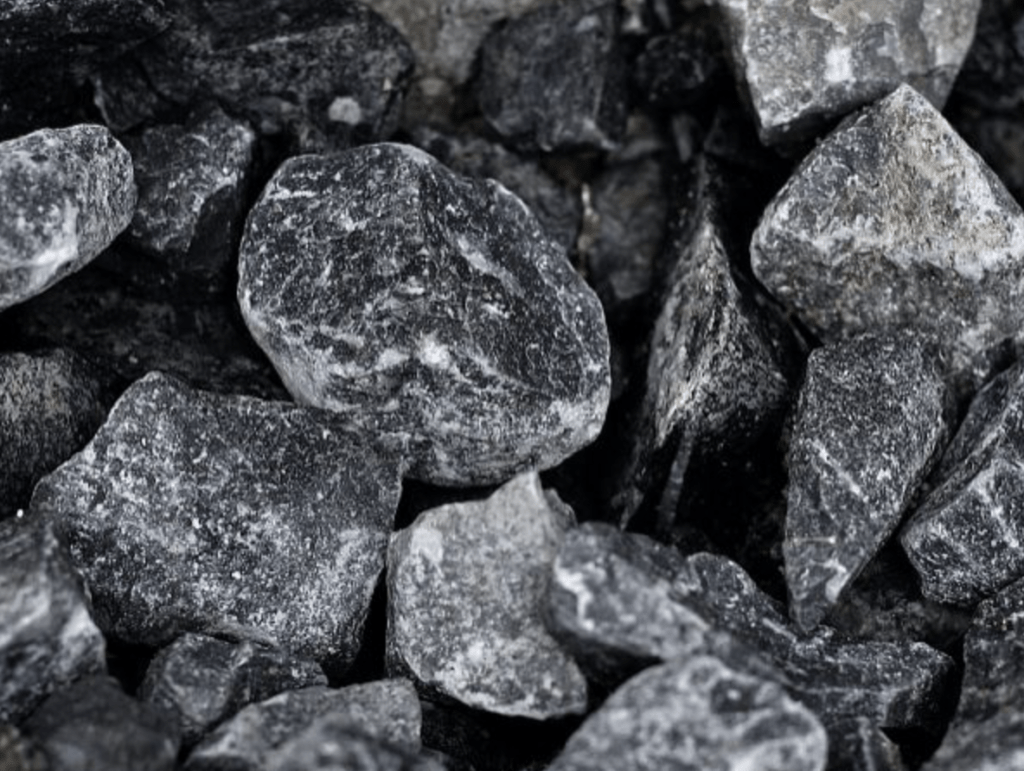
Turning silicon wafers into photovoltaic cells. Silicon wafers into cells. It is also necessary to go through a complex process of surface fusion, diffusion bonding, plasma etching, reflective coating, screen printing, rapid sintering, and so on.
Step 2: Surface Fusion
The wafers are placed in an alkaline or acidic etching solution. Millions of rough pyramid structures are formed per square centimeter on the surface of the silicon wafer. When the sunlight comes in. It creates a linear effect. So that as much sunlight as possible is trapped inside and not immediately reflected back out.
Step 3: Diffusion Bonding
PN junctions are created on the silicon wafer in a diffusion furnace. The PN junction is a special structure. It consists of an N-type and an R-type semiconductor structure. It’s this structure that allows the sun’s energy to pass through the wafer.
After diffusion is complete. Many phosphosilicate glass impurities and redundant PN structures will be formed on all surfaces and edges of the silicon wafer. Which can lead to short circuits, Which can lead to short circuits.
Step 4: Plasma Etching
Therefore, The excess structure on the wafer needs to be cleaned up by etching with an etching machine. This technology involves releasing high-energy particles in a plasma environment, inducing chemical reactions on the surface of silicon wafers. The resulting microstructures contribute to improved photovoltaic conversion efficiency, making solar cells more efficient.
Compared to traditional etching methods, plasma etching offers higher precision and controllability. It achieves finer structures, enhancing the performance of solar cells and reducing energy losses.
Step 5: Reflective Coating
After etching, The silicon wafers need to be coated, In order to reduce the reflection of sunlight on the surface of the cell, Increase the conversion efficiency of the cell,A layer of silicon nitride anti-reflective film needs to be deposited on the silicon wafer.
This film is a gas that undergoes a series of chemical reactions and plasma reactions, Silicon nitride film formed on the surface of the silicon wafer.
Photovoltaic cells look dark blue, It’s because of this solid film, Through the effects of previous steps, The surface of silicon wafers can already generate electric current when exposed to light.
Step 6: Screen Printing
It is necessary to make two positive and negative electrodes on the surface of the battery.This requires using screen printing process of photovoltaic cells.
In screen printing, ink on the printing screen is transferred to the substrate through tiny openings in the mesh, forming the desired patterns. This process typically involves printing back electrodes, front electrodes, and other functional layers.
This is an advanced process that utilizes a fine mesh screen to print conductive layers and other functional layers on solar cells. It provides a highly controllable production process for solar panels.
Step 7: Rapid Sintering
Organic resin is used in the screen printing process,The printed silicon wafer cannot be used directly, It also needs to be quickly sintered in a sintering furnace. Burn the organic resin binder, During the sintering process, It also completes various physical and chemical reactions.
This technology achieves rapid sintering by subjecting silicon wafers and thin film materials to a high-temperature environment. The brief exposure to high temperatures facilitates a quick and robust bond between the silicon wafer and thin film, enhancing the performance of solar cells.
A complete solar photovoltaic cell is not manufactured until here. Then put the individual battery pieces one by one. Series connection by welding Bottom layer inspection laminate assembly. In this way, a complete solar photovoltaic cell is assembled.
Related Blogs
Share Via:
Get in Touch with Us Now!
Got questions or feedback? We’d love to hear from you! Just fill out the form below, and our friendly team will respond ASAP.